Maxx™ Is the New Mil-Spec Lubricant
for the U.S.Military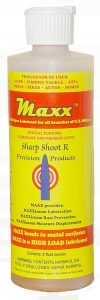
(ALL BRANCHES)
for All Small Arms including Fully Automatic Weapons
NOW AVAILABLE IN a 14 ounce AEROSOL or a CONVENIENT 8 ounce squeeze bottle
Military Small Arms – MIL_PRF_32033
Maxximum Lubrication
Maxximum Corrosion Protection
Maxximum Moisture Protection
Maxximum Reduction of Friction
Military Small Arms – MIL_PRF_32033
Shooters and outdoorsmen have problems unique to their particular sport. Firearms encounter explosive heat, grit, sand, corrosion, unburned powder residue, primer residue, carbon, minute metal fragments, and moisture as a routine part of normal use. Firearms also need to have long-term protection from rust and corrosion, as well as adequate lubrication.
With that set of problems in mind SharpShoot_R Precision began a search for a special purpose lubricant that meets the specific needs of the shooting public.
How it works:
Maxx ™ is a cutting edge product. It contains a patented particulant contained in no other commercial lubricants. This use of this particulant is protected by a patent. One of the smallest particulants used in lubricants is molybdenum. The particulant in molybdenum is approximately 2 microns in diameter. Maxx™ contains a patented particulant that is spherical in structure, and is less than 1/20 th of a micron in diameter. The minute size of this particulant greatly decreases friction and drag by reducing greatly the build_up of heat. It puts an ultra_thin layer of spherical particulant and a high heat tolerant lubricant between metal parts. The small diameter of this particulant allows Maxx™ to penetrate in to the terrain of metal surfaces, which are less than 1/20 th of a micron deep. This particulant further carries with it a unique blend of synthetic non_petroleum low drag lubricant and high lubricity natural oils that sets up a boundary shield of lubrication.
Properties:
The characteristics of this natural/synthetic blend lubricant are quite unique, in that they have an operating range of +600º F down to _70º F. Being a synthetic base lubricant, Maxx™ is non_gumming, and non_shellacing over any length of time. It does not change in viscosity or color, over time. Maxx™ contains no teflon or PTFE of any kind. These products have proven themselves to be gumming agents a which build up, and actually prevent lubrication to take place.
TECHNICAL BULLETIN:
How to use Maxx ™:
Maxx™ works in a truly unique manner. It is applied in two or three applications after a thorough degreasing solvent is used. It is necessary to remove all evidence of other lubricants to make Maxx™ totally effective. Apply Maxx™ to a clean firearm and allow the volatiles to vaporize for 5 minutes or so. Apply a second application and repeat the drying procedure. This allows Maxx™ to build a coating over the metal of around 20 to 25 microns in thickness. It is this film that provides maximum lubrication while cutting friction to an absolute minimum. Maxx™ has proven itself superior in all the testing done by the U.S. Military and has been adopted as the lubricant for all small arms both semi-automatic and fully automatic.
Maxx™ has a neutral di-electric constant which allows the product to lubricate without attracting dirt and grit. Most lubricants are either positive or negative charged which is an attractant to dust particles. The neutral di-electric constant properties also allow Maxx™ to be used in any application where electric polarity is a concern.
Maxx™ is also a boon to users because if it’s moisture displacing qualities. Maxx™ will force moisture out of any metal or electrical parts and provide both lubrication and corrosion protection.
Maxx™ proved itself a superior anti-corrosion product in the testing done by the U.S. Military. A film of Maxx™ was put on metal parts to be tested, then a 5% solution of salt spray coated the test parts and the temperature was raised to 95 degrees. Maxx™ coated parts went for over 1000 hours with no rust or corrosion.
Maxx™ is available in 2 convenient sizes a 14 ounce can and a 8 ounce bottle.
Maxx™ MAX-140 suggested retail price for the 14 ounce can
Maxx™ MAX-008 suggested retail price for the 8 ounce can
Refer to price list for pricing
Please check out our price list and catalog!
FOR FORMATION ON THE NEAREST DEALER OR DISTRIBUTOR PLEASE CALL OR E-MAIL US.
Sharp Shoot R Precision Products
Box 171
Paola, Kansas 66071
785-883-4444 Phone
785-883-2525 Fax
Email: [email protected]
TESTIMONIAL MAY 2015
Sender’s name:
Bob Fortunato
E-mail: [email protected]
Phone: on request
Message:
I’ve been using both SLICKER and MAXX since October of 2014. These are my observations:
On the BOLT BODY, LOCKING LUGS and REAR LUG of both of my Benchrest Rifles( KELBLY PANDA and a STILLER VIPER.
I used both of these Rifles for WINTER LEAGUE here at THE CAMILLUS SPORTSMEN”S CLUB.
The bolts and treated parts stayed lubed up into APRIL of 2015 when I re-treated them(not because I had to).
The LUBRICITY provided by the SLICKER and MAXX is far superior to any gun grease or oil I have ever used.
I then decided to try it on my MACHINERY and TOOLS,
On the WAYS of my SOUTH BEND HEAVY 10 LATHE and the CRANKS..
They are still smooth since being treated in NOVEMBER 2014.
I used them on my BRIDGEPORT “M” HEAD MILL (on the QUILL surfaces)
It is much easier to operate and VERY SMOOTH.
No sign of wear yet. In my opinion:
THESE ARE GREAT PRODUCTS that work for FIREARM and INDUSTRIAL APPLICATIONS.
U.S. Government Requirements and Specification Information
THE FOLLOWING IS JUST A SMALL PART OF U.S.GOVERNMENT REQUIREMENTS FOR THE CRITERIA ESTABLISHED FOR SMALL ARMS LUBRICANT ( WHICH INCLUDES SEMI-AUTO AND FULL -AUTO WEAPONS AND WEAPONS SYSTEMS.
MIL-PRF-32033, 24 July 2000 , SUPERSEDING, VV-L-800C
May 11, 1983
PERFORMANCE SPECIFICATION
LUBRICATING OIL, GENERAL PURPOSE, PRESERVATIVE
(WATER-DISPLACING, LOW TEMPERATURE)
This specification is approved for use by all Departments and Agencies of the
Department of Defense.
1. SCOPE.
1.1 Scope. This specification covers one type and grade of water-displacing, preservative
lubricating oil, known hereinafter as “oil”, for general purpose applications at low temperatures.
The oil can be applied by dipping, brushing, or by spraying from gas-pressurized cans. The oil is
identified by Military Symbol PL-S and NATO Code Number O-190.
2. APPLICABLE DOCUMENTS
2.1 General. The documents listed in this section are specified in sections 3 and 4 of this
specification. This section does not include documents cited in other sections of this specification
or recommended for additional information or as examples. While every effort has been made to
ensure the completeness of this list, document users are cautioned that they must meet all
specified requirements in documents cited in sections 3 and 4 of this specification, whether or not
they are listed.
Beneficial comments (recommendations, additions, deletions) and any pertinent data which may
be of use in improving this document should be addressed to: U.S. Army Tank-automotive and
Armaments Command, ATTN: AMSTA-TR-D/210, Warren, MI 48397-5000, by using the
Standardization Document Improvement Proposal (DD Form 1426) appearing at the end of this
document or by letter.
AMSC N/A FSC 9150
DISTRIBUTION STATEMENT A. Approved for public release, distribution is unlimited.
MIL-PRF-32033
2
2.2 Government documents.
2.2.1 Specifications, standards and handbooks. The following specifications, standards,
and handbooks form a part of this document to the extent specified herein. Unless otherwise
specified, the issue of these documents shall be those listed in that issue of the Department of
Defense Index of Specifications and Standards (DoDISS) and supplement thereto, cited in the
solicitation (see 6.2).
SPECIFICATIONS
DEPARTMENT OF DEFENSE
MIL-PRF-680 – Degreasing Solvent.
STANDARDS
FEDERAL
FED-STD-791 – Lubricants, Liquid Fuels, and Related Products;
Methods of Testing.
(Unless otherwise indicated, copies of the above specifications, standards, and handbooks
are available from the Standardization Document Order Desk, 700 Robbins Avenue, Building 4D,
Philadelphia, PA 19111-5094.)
2.2.2 Other Government documents, drawings, and publications. The following other
Government document forms a part of this document to the extent specified herein. Unless
otherwise specified, the issues are those cited in the solicitation.
AMERICAN CONFERENCE OF GOVERNMENTAL INDUSTRIAL HYGIENISTS (ACGIH)
Threshold Limit Values and Biological Indices
(Application for copies should be addressed to the American Conference of Governmental
Industrial Hygienists, 1330 Kemper Meadow Drive, Cincinnati, OH 45240 or website:
http://www.acgih.org)
DEPARTMENT OF LABOR (DOL)
OSHA 29 CFR 1910.1200 – Hazard Communication Interpretation Regarding
Lubricating Oils.
(Requests for copies of the Code of Federal Regulations (CFR) Guideline may be obtained
from the Superintendent of Documents, US Government Printing Office, Washington, DC 20402.)
MIL-PRF-32033
3
NATIONAL TOXICOLOGY PROGRAM
– Annual Report on Carcinogens.
(Requests for copies should be addressed to the Annual Report on Carcinogens, National
Toxicology Program, PO Box 12233, Research Triangle Park, NC 27709.)
2.3 Non-Government publications. The following documents form a part of this
document to the extent specified herein. Unless otherwise specified, the issues of the documents
which are DoD adopted are those listed in the issue of the DODISS cited in the solicitation.
Unless otherwise specified, the issues of documents not listed in the DoDISS are the issues of the
documents cited in the solicitation (see 6.2).
AMERICAN SOCIETY FOR TESTING AND MATERIALS (ASTM)
ASTM D91 – Precipitation Number of Lubricating Oils
(DoD Adopted).
ASTM D92 – Flash and Fire Points by Cleveland Open Cup
(DoD Adopted).
ASTM D97 – Pour Point of Petroleum Products (DoD Adopted).
ASTM D130 – Detection of Copper Corrosion from Petroleum
Products by the Copper Strip Tarnish Test
(DoD Adopted).
ASTM D445 – Kinematic Viscosity of Transparent and Opaque
Liquids (the Calculation of Dynamic Viscosity)
(DoD Adopted).
ASTM D972 – Evaporation Loss of Lubricating Greases and Oils
(DoD Adopted).
ASTM D974 – Acid and Base Number by Color-Indicator Titration
(DoD Adopted).
ASTM D1152 – Methanol (Methyl Alcohol).
ASTM D1500 – ASTM Color of Petroleum Products (ASTM Color
Scale) (DoD Adopted).
ASTM D1748 – Rust Protection by Metal Preservatives in the
Humidity Cabinet (DoD Adopted).
ASTM D4172 – Wear Preventive Characteristics of Lubricating Fluid
(Four-Ball Method) (DoD Adopted).
(Application for copies should be addressed to the American Society for Testing and
Materials, 100 Barr Harbor Drive, Conshohocken, PA 19428-2959.)
MIL-PRF-32033
4
2.4 Order of precedence. In the event of a conflict between the text of this document and
the references cited herein, the text of this document takes precedence. Nothing in this document,
however, supersedes applicable laws and regulations unless a specific exemption has been obtained.
3. REQUIREMENTS
3.1 Qualification. The lubricants furnished under this specification shall be products that
are authorized by the qualifying activity for listing on the applicable qualified products list (QPL)
before contract award (see 4.1.1, and 6.3). Any change in the formulation of a qualified product
will necessitate its requalification (see 6.9).
3.2 Materials. Unless otherwise specified herein, the chemical formula of the oil is the
prerogative of the contractor as long as all articles submitted to the Government fully meet the
operating, interface, support and ownership, and environmental requirements specified.
3.2.1 Recycled, recovered, or environmentally preferable materials. Recycled, recovered,
or environmentally preferable materials should be used to the maximum extent possible provided
that the material meets or exceeds the operational and maintenance requirements, and promotes
economically advantageous life cycle costs.
3.3 Operating requirements.
3.3.1 Kinematic viscosity. The kinematic viscosity of the oil shall be as specified in table I
(see 4.2.2.1).
TABLE I. Kinematic viscosity.
Kinematic viscosity, centistokes (cSt)
@ 40 degrees Celsius (ºC), minimum. 11
@ -40°C, maximum. 7,000
@ -54°C, maximum. 60,000
3.3.2 Corrosion protection (humidity cabinet). The oil shall protect metal to the extent that
no more than a combined total of three corrosion dots, none of which exceed 1 millimeter (mm) in
diameter, occur on the panels (see 4.2.2.2).
3.3.2.1 Removability. The oil shall leave no visual evidence of oil residue, stain or
discoloration on metals (see 4.2.2.2.1).
3.3.3 Water displacement and water stability. The oil, after storage in contact with water,
shall satisfactorily displace water as evidenced by the absence of rust, mottling, or surface stains
on the panels (see 4.2.2.3).
MIL-PRF-32033
5
3.3.4 Corrosiveness (bimetallic couple). The oil shall protect metal to the extent that no
more than a combined total of three corrosion dots, none of which exceed 1 mm in diameter,
occur on the discs (see 4.2.2.4).
3.3.5 Wear. The oil shall lubricate the steel balls such that the average scar diameter on
the steel balls shall not exceed 1 mm (see 4.2.2.5).
3.4 Interface requirements.
3.4.1 Copper strip corrosion. The oil shall not tarnish the copper strip exceeding the
value of 2a on the ASTM Copper Strip Corrosion Standards (see 4.2.3.1).
3.4.2 Corrosiveness and oxidation stability (metal protection). The oil shall not produce
corrosion or oxidation effects on metal specimens greater than a weight gain or loss of
0.2 milligrams/square centimeter (mg/cm2). The oil shall not pit nor etch the surface of the metal
specimens. The oxidized oil shall exhibit no insoluble materials or gum when examined
(see 4.2.3.2).
3.4.2.1 Viscosity stability. The viscosity change of the oxidized oil at 40°C shall be not
more than a 5 percent (%) decrease or a 20% increase (see 4.2.3.2.1).
3.4.2.2 Neutralization number change. The neutralization number of the oxidized oil shall
not be more than 0.20 higher than the initial neutralization number of unoxidized oil
(see 4.2.3.2.2).
3.4.3 Color. The ASTM Color of the oil shall not be greater than 7.0 (see 4.2.3.3).
3.5 Support and ownership requirements.
3.5.1 Solid sediment/precipitation number. The oil shall generate not more than
0.05 milliliters (mL) mean total volume of sediment (see 4.2.4.1).
3.5.2 Toxicity. The oil shall have no adverse (injurious or damaging) effects on human
health when it is used as intended (see 6.1). Blenders, formulators, and suppliers shall follow the
guidelines of OSHA 29 CFR 1910.1200, the ACGIH Threshold Limit Values and Biological
Indices, and the most current National Toxicology Program’s Annual Report on Carcinogens
(see 4.2.4.2).
3.5.3 Product identification. Each unit container and its exterior package shall be labeled
as follows (see 4.2.4.3):
MIL-PRF-32033
6
LUBRICATING OIL, GENERAL PURPOSE, PRESERVATIVE
WARNING!
*DO NOT USE THIS OIL IN THE PROCESSING OR HANDLING EQUIPMENT OR SURFACE THAT
MAY CONTACT FOOD!
*DO NOT ALLOW THE OIL TO CONTAMINATE FOODSTUFF!
*DO NOT USE THIS OIL IN ANY FUEL SYSTEM OR COMBUSTION CHAMBER OF ENGINES!
3.5.3.1 Warning for gas-pressurized cans. In addition to the marking specified in 3.5.3,
oil supplied in gas-pressurized cans shall be marked as follows:
WARNING!
CONTENTS UNDER PRESSURE
*DO NOT STORE THIS CAN ABOVE 49°C (120°F)!
*KEEP AWAY FROM DIRECT SUNLIGHT, RADIATORS, STOVES, HOT WATER, OR OTHER HEAT
SOURCES!
*DO NOT PUNCTURE THIS CAN NOR PLACE IT IN AN INCINERATOR!
3.5.4 Fill (gas-pressurized cans only). The oil supplied in gas-pressurized cans shall have
a minimum net weight of 12.5 ounces (see 4.2.4.4).
3.6 Environmental requirements.
3.6.1 Flash point. The minimum flash point of the oil shall be 135°C (see 4.2.5.1).
3.6.2 Pour point. The maximum pour point of the oil shall be –57°C (see 4.2.5.2).
3.6.3 Evaporation loss. The maximum mass percent evaporation loss of the oil shall be
25% (see 4.2.5.3).
3.6.4 Low temperature stability. The oil shall show no evidence of gelling, crystallization,
solidification or separation of insoluble material when subjected to a temperature of -45°C for 72
hours (see 4.2.5.4).
3.6.5 Film characteristics/high temperature stability. The oil shall show no evidence of
becoming gummy, tacky, or hard when subjected to a temperature of 100°C for 24 hours
(see 4.2.5.5).
MIL-PRF-32033
7
4. VERIFICATION
4.1 Classification of inspections. The inspection requirements specified herein are
classified as follows:
a. Qualification inspection (see 4.1.1).
b. Conformance inspection (see 4.1.2).
4.1.1 Qualification inspection. Qualification inspection shall consist of tests for all of the
requirements specified in section 3 and may be conducted in any plant or laboratory approved by
the qualifying activity (see 6.3).
4.1.2 Conformance inspection. Conformance inspection consists of tests for all of the
requirements specified in section 3 and may be conducted in any plant or laboratory approved by
the qualifying activity.
4.2 Verification methods. Acceptable verification methods included in this section are
visual inspection, and measurement, sample tests, full-scale demonstration tests, simulation,
modeling, engineering evaluation, component properties analysis, and similarity to previously
approved or previously qualified designs.
4.2.1 Verification alternatives. The manufacturer may propose alternative test methods,
techniques, or equipment, including the application of statistical process control, tool control, or
cost effective sampling procedures to verify performance. See the contract for alternatives that
replace verification methods required by this specification.
4.2.2 Operating requirements verifications.
4.2.2.1 Kinematic viscosity. To determine conformance to 3.3.1, the oil shall be tested in
accordance with (IAW) ASTM D445, and exhibit a kinematic viscosity within the range specified
in table I.
4.2.2.2 Corrosion protection (humidity cabinet). To determine conformance to 3.3.2, the
oil shall be tested IAW ASTM D1748, and shall pass (see 6.8).
4.2.2.2.1 Removability. To determine conformance to 3.3.2.1, the oil shall be tested by
completely immersing the three oil-coated test panels used for the humidity cabinet test
(see 4.2.2.2) in a breaker containing degreasing solvent IAW MIL-PRF-680 at 25°C and agitating
the solvent slightly for not more than one minute. Then, repeat this process with methanol IAW
ASTM D 1152. After removal from the solvent, the test panels shall not evidence any oil residue,
stain, or discoloration.
MIL-PRF-32033
8
4.2.2.3 Water displacement and water stability. To determine conformance to 3.3.3, the
oil shall be tested IAW method 3007 of FED-STD-791. There shall be no evidence of rust,
mottling, or surface stains on the panels following the test.
4.2.2.4 Corrosiveness (bimetallic couple). To determine conformance to 3.3.4, the oil
shall be tested IAW method 5322 of FED-STD-791. There shall be no evidence of rust, mottling,
or surface stains on the panels following the test.
4.2.2.5 Wear. To determine conformance to 3.3.5, the oil shall be tested IAW
ASTM D4172. Following the test, the average scar diameter on the steel balls shall not exceed
1 mm.
4.2.3 Interface requirements verifications.
4.2.3.1 Copper strip corrosion. To determine conformance to 3.4.1, the oil shall be
tested IAW ASTM D130 for 3 hours at 100°C. The copper strips shall exhibit a value not more
than 2a IAW the ASTM Copper Strip Corrosion Standards.
4.2.3.2 Corrosiveness and oxidation stability (metal protection). To determine
conformance to 3.4.2, the oil shall be tested IAW method 5308 of FED-STD-791. The oil shall
not produce corrosion or oxidation effects on metal specimens greater than a weight gain or loss
of 0.2 mg/cm2, nor pitting or etching of the surfaces. The oxidized oil shall not evidence any
insoluble materials or gum.
4.2.3.2.1 Viscosity stability. To determine conformance to 3.4.2.1, after completing the
corrosiveness and oxidation stability test (see 4.2.3.2), determine the viscosity of the oil sample at
40°C IAW ASTM D445. The calculated viscosity change, based on the original viscosity of the
oil, shall be not more than a 5% decrease or a 20% increase.
4.2.3.2.2 Neutralization number change. To determine conformance to 3.4.2.2, after
completing the corrosiveness and oxidation stability test (see 4.2.3.2), determine the
neutralization number of the oil IAW ASTM D974. The neutralization number shall not be more
than 0.20 higher than the original neutralization number of the oil.
4.2.3.3 Color. To determine conformance to 3.4.3, the oil shall be tested IAW
ASTM D1500, and shall exhibit a color not greater than 7.0.
4.2.4 Support and ownership requirements verifications.
4.2.4.1 Solid sediment/precipitation number. To determine conformance to 3.5.1, the oil
shall be tested IAW ASTM D91, and shall generate not more than 0.5 mL mean total volume of
sediment.
MIL-PRF-32033
9
4.2.4.2 Toxicity. To determine conformance to 3.5.2, components of the oil’s
formulation shall be compared with the toxic limits established by the guidelines of OSHA
29 CFR 1910.1200, the ACGIH Threshold Limit Values and Biological Indices and the most
current National Toxicology Program’s Annual report on Carcinogens. Oils with components
exceeding the toxic limits shall be disqualified. Methods of quantitative determination shall be
selected at the discretion of both the qualifying activity and the manufacture/blender.
4.2.4.3 Product identification. To determine conformance to 3.5.3 and 3.5.3.1, the oil
unit containers shall be examined for the proper product warning/identification.
4.2.4.4 Fill (gas-pressurized cans only). To determine conformance to 3.5.4, a can of the
oil shall be weighed. The oil shall be sprayed from the can in three-minute periods, followed by
one minute pauses, until the can is empty. The can shall then be re-weighed, and the net weight
calculated. The calculated net weight shall not be less than 12.5 ounces.
4.2.5 Environmental requirements verifications.
4.2.5.1 Flash point. To determine conformance to 3.6.1, the oil shall be tested IAW
ASTM D92, and shall exhibit a minimum flash point of 135°C.
4.2.5.2 Pour point. To determine conformance to 3.6.2, the oil shall be tested IAW
ASTM D97, and shall exhibit a maximum pour point of –57°C.
4.2.5.3 Evaporation loss. To determine conformance to 3.6.3, the oil shall be tested at
100°C IAW ASTM D972, and shall exhibit a maximum mass percent evaporation loss of 25%.
4.2.5.4 Low temperature stability. To determine conformance to 3.6.4, the oil shall be
tested at -45°C IAW method 3458 of FED-STD-791, and shall not exhibit any gelling,
crystallization, solidification or separation of insoluble material.
4.2.5.5 Film characteristics/high temperature stability. To determine conformance to
3.6.5, coat a glass panel or a microscope slide with a sample of the oil. Next, drain the panel for
24 hours at an angle of 45° with the horizontal and at a temperature of 25° ± 3°C. Then store the
panel in an oven at 100°C for 24 hours. The oil shall not exhibit any gumminess, tackiness or
hardness.
5. PACKAGING
5.1 Packaging. For acquisition purposes, the packaging requirements shall be as specified
in the contract or order (see 6.2). When actual packaging of material is to be performed by DoD
personnel, these personnel need to contact the responsible packaging activity to ascertain requisite
packaging requirements. Packaging requirements are maintained by the Inventory Control Point’s
MIL-PRF-32033
10
packaging activity within the Military Department or Defense Agency, or within the Military
Department’s System Command. Packaging data retrieval is available from the managing Military
Department’s or Defense Agency’s automated packaging files, CD-ROM products, or by
contacting the responsible packaging activity.
6. NOTES
(This section contains information of a general or explanatory nature which may be
helpful, but is not mandatory.)
6.1 Intended use. The lubricating oil, general purpose, preservative, is intended for
lubrication and protecting against corrosion of certain small arms and automatic weapons and
whenever a general purpose, water-displacing, low-temperature lubricating oil is required. This
oil becomes very viscous at low temperatures so that its use at temperatures below -40°C is
limited by a number of machine design factors and should be proved for any specific item
application by test before adoption. The availability of this material in gas-pressurized containers
will prove to be beneficial for use in areas difficult to preserve by existing procedures. This
preservative oil should not be used to protect the fuel system and combustion chamber of engines
which are preserved in accordance with standard procedures. This material contains a carboxylic
acid which could react with certain metals present in the fuel system, forming soaps which could
contribute to fuel filter plugging.
6.2 Acquisition requirements. Acquisition documents must specify the following:
a. Title, number, and date of this specification.
b. Issue of DoDISS to be cited in the solicitation, and if required, the specific issue of
individual documents referenced (see 2.2.1 and 2.3).
c. Location of verification testing (see 4.1).
d. Packaging requirements (see 5.1).
6.3 Qualification. With respect to products requiring qualification, awards will be made
only for products which are, at the time of award of contract, qualified for inclusion in Qualified
Products List QPL No. 800 whether or not such products have actually been so listed by that
date. The attention of the contractors is called to these requirements, and manufacturers are
urged to arrange to have the products that they propose to offer to the Federal Government tested
for qualification in order that they may be eligible to be awarded contracts or purchase orders for
the products covered by this specification. Information pertaining to qualification of products
may be obtained from: Department of the Army, U.S. Tank-automotive and Armaments
Command, F & L Technology Team, ATTN: AMSTA-TR-D/210, Warren, Michigan
48397-5000.
MIL-PRF-32033
11
6.4 Definitions.
6.4.1 Film characteristics. A drying process progresses through three stages identified as
gummy, tacky, and hard. These are defined as follows:
a. Gummy – First evidence of becoming viscous.
b. Tacky – Advanced stage of drying, becoming sticky.
c. Hard – A completely dry-to-touch film.
6.5 International standardization. Certain provisions of this specification are the subject
of international standardization agreements (NATO STANAGs 1135 and 7094). When
amendment, revision, or cancellation of this specification is proposed which would affect or
violate the international agreement concerned, the preparing activity will take appropriate
reconciliation action through international standardization channels, including departmental
standardization offices, as required.
6.6 Waste disposal instructions.
6.6.1 Recovery (RC). The very first step in disposal is to coordinate with Defense
Property Disposal Office (DPDO) for turn-in for disposal of any excess items of supply. Defense
Disposal Manual DOD 4160.21-M (with pertinent supplements/messages) describes the
requirements for such turn-ins. Variations exist whether the DPDO accepts physical custody of
the disposal turn-in. The potential for DPDO acceptance and disposal processing is enhanced by
comprehensive identification. If the DPDO does not accept the item for disposal (accountability)
or returns the item to the generator for disposal, the manufacturer/supplier should be contacted
for chemical recovery before proceeding with ultimate disposal management procedures.
DISCLAIMER
THE RECOMMENDED DISPOSAL INSTRUCTION IS FORMULATED FOR USE BY
ELEMENTS OF THE DEPARTMENT OF DEFENSE. THE UNITED STATES OF
AMERICA IN NO MANNER WHATSOEVER EXPRESSLY OR IMPLIEDLY
WARRANTS, STATES, OR INTENDS SAID INSTRUCTION TO HAVE ANY
APPLICATION, USE, OR VIABILITY BY OR TO ANY PERSON OR PERSONS
OUTSIDE THE DEPARTMENT OF DEFENSE NOR ANY PERSON OR PERSONS
CONTRACTING WITH ANY INSTRUMENT OF THE UNITED STATES OF AMERICA
AND DISCLAIMS ALL LIABILITY FOR SUCH USE. ANY PERSON UTILIZING THIS
INSTRUCTION WHO IS NOT A MILITARY OR CIVILIAN EMPLOYEE OF THE
UNITED STATES OF AMERICA SHOULD SEEK COMPETENT PROFESSIONAL
ADVICE TO VERIFY AND ASSUME RESPONSIBILITY FOR THE SUITABILITY OF
THIS INSTRUCTION TO THEIR PARTICULAR SITUATION REGARDLESS OF
SIMILARITY TO A CORRESPONDING DEPARTMENT OF DEFENSE OR OTHER
GOVERNMENT SITUATION.
MIL-PRF-32033
12
6.7 Material Safety Data Sheets (MSDS). Contracting officers will identify those
activities requiring copies of MSDS’s prepared in accordance with FED-STD-313. The pertinent
Government mailing addresses for submission of data are listed in FED-STD-313; and
29 CFR 1910.1200 requires that the MSDS for each hazardous chemical used in an operation
must be readily available to personnel using the material. Contracting officers will identify the
activities requiring copies of the MSDS.
6.8 Panel preparation for oil in gas-pressurized cans. Historically, the following
procedure has been found to provide the best results for humidity cabinet testing of oil supplied in
gas-pressurized cans (see 3.3.2 and 4.2.2.2):
Shake a gas-pressurized can of oil vigorously for 30 seconds. Set the cleaned panels at an
angle of 15° from vertical. Hold the pressurized can vertically at a distance of 25 to 30
centimeters from the panel. With the valve open, move the can to direct the spray from
one edge of the panel to the other. Make sufficient passes to assure a continuous coating.
After five minutes examine the coating to determine if it is smooth and unbroken. If the
coating shows evidence of gas entrapment, prepare another panel. Drain the panels for 2
hours and submit them to the test specified in ASTM D1748.
6.9 QPL tolerances. The oils supplied under contract should have the same formulation
as when qualified. The finished oil properties should fall within permissible tolerances as listed in
table II. After the application of tolerances, the values of the properties of the oil should not
exceed the maximum nor fall below the minimum requirements specified herein.
TABLE II. QPL tolerances.
Property Tolerance
Kinematic viscosity @ 40°C (see 3.3.1) ±1.1 cSt
Kinematic viscosity @ -40°C (see 3.3.1) ±700 cSt
Kinematic viscosity @ -54°C (see 3.3.1) ±600 cSt
Pour point (see 3.6.2) ±6ºC
Flash point (see 3.6.1) ±10ºC
Wear (scar diameter) (see 3.3.5) ±0.30 mm
Evaporation loss (see 3.6.3) ±5.0%
MIL-PRF-32033
13
6.10 Subject term (key word) listing.
Lubrication
NATO STANAGs 1135 and 7094
6.11 Changes from previous issue. Marginal notations are not used in this revision to
identify changes with respect to the previous issue due to the extent of the changes.
Custodians: Preparing Activity:
Army – AT Army – AT
Navy – AS
Air Force – 11 (Project 9150-1167)
Review Activities:
Army – AR, MI, MD, SM
Navy – MC, SA
Air Force –03, 50, 68
DLA – GS, PS
STANDARDIZATION DOCUMENT IMPROVEMENT PROPOSAL
INSTRUCTIONS
I RECOMMEND A CHANGE:
1. DOCUMENT NUMBER
2. DOCUMENT DATE (YYYYMMDD)
3. DOCUMENT TITLE
4. NATURE OF CHANGE (Identify paragraph number and include proposed rewrite, if possible. Attach extra sheets as needed.)
5. REASON FOR RECOMMENDATION
6. SUBMITTER
a. NAME (Last, First, Middle Initial)
b. ORGANIZATION
c. ADDRESS (Include Zip Code)
d. TELEPHONE (Include Area Code)
(1) Commercial
(2) DSN
(If applicable)
7. DATE SUBMITTED (YYYYMMDD)
8. PREPARING ACTIVITY
a. NAME
b. TELEPHONE (Include Area Code)
(1) Commercial (2) DSN
(810) 574-8745 786-8745
c. ADDRESS (Include Zip Code)
Commander
U.S. Army Tank-automotive and Armaments Command
ATTN: AMSTA-TR-E/IE
Warren, MI 48397-5000
IF YOU DO NOT RECEIVE A REPLY WITHIN 45 DAYS, CONTACT:
Defense Standardization Program Office (DLSC-LM)
8725 John J. Kingman Road, Suite 2533
Fort Belvoir, Virginia 22060-6221
Telephone (703) 767-6888 DSN 427-6888
1. The preparing activity must complete blocks 1, 2, 3, and 8. In block 1, both the document number and revision letter
should be given.
2. The submitter of this form must complete blocks 4, 5, 6, and 7, and send to preparing activity.
3. The preparing activity must provide a reply within 30 days from receipt of the form.
NOTE: This form may not be used to request copies of documents, nor to request waivers, or clarification of
requirements on current contracts. Comments submitted on this form do not constitute or imply authorization to waive
any portion of the referenced document(s) or to amend contractual requirements.
DD FORM 1426, FEB 1999 (EG) WHS/DIOR, Feb 99 PREVIOUS EDITION IS OBSOLETE.
MIL-PRF-32033 20000724
LUBRICATING OIL, GENERAL PURPOSE, PRESERVATIVE (WATER-DISPLACING, LOW TEMPERATURE)
MIL-PRF-32033
AMENDMENT 1
27 June 2001
PERFORMANCE SPECIFICATION
LUBRICATING OIL, GENERAL PURPOSE, PRESERVATIVE
(WATER-DISPLACING, LOW TEMPERATURE)
This amendment forms a part of MIL-PRF-32033, dated 24 July 2000, and is approved
for use by all Departments and Agencies of the Department of Defense.
PAGE 8
4.2.4.1: Delete and substitute:
“4.2.4.1 Solid sediment/precipitation number. To determine conformance to 3.5.1, the
oil shall be tested IAW ASTM D91, and shall not generate more than 0.05 mL mean total
volume of sediment.”
Custodians: Preparing Activity:
Army – AT Army – AT
Navy – AS
Air Force – 11 (Project 9150-1267)
Review Activities:
Army – AR, MI, MD, SM
Navy – MC, SA
Air Force – 03, 50, 68
DLA – GS, PS
AMSC N/A 1 of 1 FSC 9150
DISTRIBUTION STATEMENT A. Approved for public release, distribution is unlimited.